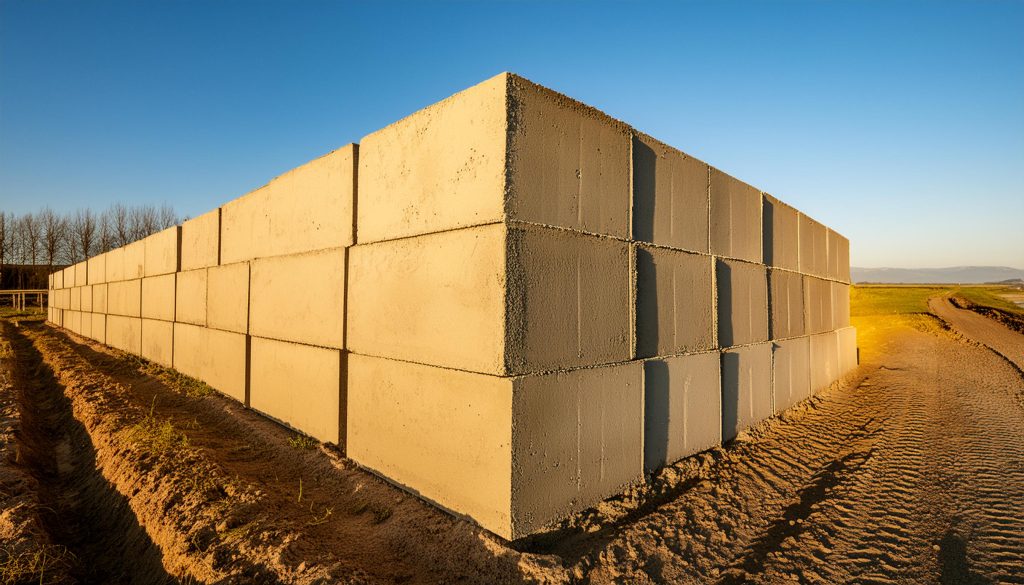
What is Lightweight Concrete?
Lightweight concrete is a revolutionary building material that offers numerous benefits over traditional concrete, making it an increasingly popular choice in construction and DIY projects alike. Known for its reduced density, lightweight concrete is made by incorporating lightweight aggregates such as expanded clay, shale, or perlite. This innovative mix results in a material that retains the strength and durability of conventional concrete while being significantly lighter and easier to work with. The versatility of lightweight concrete allows for its use in a wide range of applications, from structural elements in buildings to decorative items like planters and sculptures.
The concept of lightweight concrete dates back to ancient times when the Romans used pumice, a naturally occurring lightweight aggregate, in their construction projects. Modern advancements in material science have refined the process, allowing for more consistent and reliable lightweight concrete mixtures. Today, lightweight concrete is celebrated not only for its functional benefits but also for its environmental advantages, as it often incorporates recycled materials and reduces the overall carbon footprint of construction projects. In this article, we will delve into what lightweight concrete is, its benefits, and how it can be used effectively in various projects.
Understanding Lightweight Concrete
Lightweight concrete is a specialized form of concrete that incorporates lightweight aggregates to reduce its overall density. Traditional concrete typically has a density of about 2400 kg/m³, whereas lightweight concrete has a density ranging from 300 to 1800 kg/m³, depending on the mix and intended use. The reduction in weight is achieved by using materials such as expanded clay, pumice, perlite, or vermiculite instead of the heavier gravel and sand used in standard concrete. The concept of lightweight concrete dates back to ancient times when Romans used pumice as an aggregate in their construction projects. Modern advancements in material science have refined the process, allowing for more consistent and reliable lightweight concrete mixtures.
Key Benefits of Lightweight Concrete
- Reduced Structural Load: One of the primary advantages of lightweight concrete is its lower weight, which significantly reduces the load on structural elements. This is particularly beneficial in high-rise buildings and structures where reducing weight can lead to savings in foundation costs and overall construction materials.
- Improved Insulation: Lightweight concrete provides excellent thermal and acoustic insulation properties. Its porous nature helps in maintaining consistent indoor temperatures, reducing heating and cooling costs. Additionally, it offers soundproofing benefits, making it ideal for residential and commercial buildings in noisy environments.
- Ease of Handling and Installation: The reduced weight of lightweight concrete makes it easier to transport, handle, and install, which can lead to faster construction times and lower labor costs. This is especially advantageous for DIY projects and situations where heavy lifting equipment is not available.
- Versatility in Design: Lightweight concrete can be molded into a variety of shapes and sizes, making it suitable for both structural and decorative applications. It is commonly used in precast panels, blocks, and even intricate architectural elements.
- Eco-Friendly Options: Many lightweight concrete mixtures incorporate recycled materials, such as fly ash or slag, which contribute to sustainability. The use of less raw material also reduces the overall carbon footprint of construction projects.
- Durability and Strength: Despite its lighter weight, lightweight concrete can achieve comparable strength to traditional concrete. When properly designed and cured, it offers long-lasting durability and resistance to weathering and chemical attack.
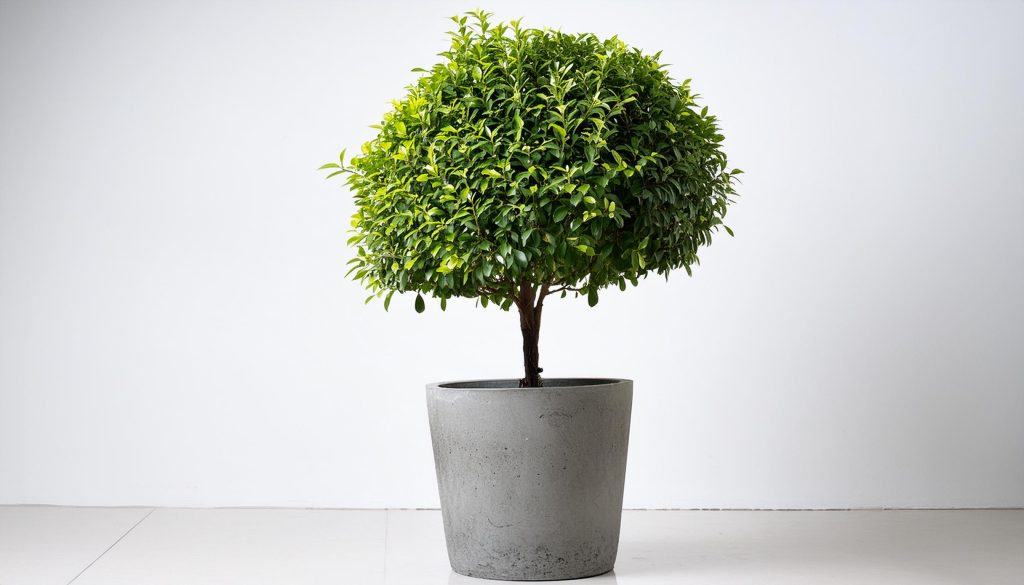
Common Uses and Applications
Lightweight concrete is used in a variety of applications across different industries, owing to its unique properties and versatility. Here are some detailed uses and applications:
- Building Construction:
- Load-Bearing Walls: Lightweight concrete is frequently used in the construction of load-bearing walls. Its reduced weight helps decrease the overall load on the structure’s foundation, which can lead to significant cost savings in terms of foundation materials and construction time.
- Floors and Roofs: In multi-story buildings, the use of lightweight concrete for floors and roofs can reduce the weight of each level, allowing for taller buildings without the need for excessive structural support. This reduction in weight also means that lighter and less expensive framing materials can be used.
- Partitions and Non-Load-Bearing Walls: Lightweight concrete is ideal for internal partitions and non-load-bearing walls. Its acoustic insulation properties help in reducing noise transmission between rooms, making it perfect for residential and commercial buildings.
- Insulation Panels:
- Thermal Insulation: Lightweight concrete’s porous nature makes it an excellent insulator. It is commonly used in the production of insulation panels that help maintain consistent indoor temperatures, reducing the need for additional heating or cooling. This results in energy savings and improved comfort levels within buildings.
- Acoustic Insulation: Its ability to absorb sound makes lightweight concrete suitable for acoustic insulation panels. These panels are used in buildings to reduce noise levels, creating quieter indoor environments, especially in areas exposed to high levels of external noise like urban centers or near highways.
- Soundproofing:
- Walls and Floors: Lightweight concrete’s inherent soundproofing qualities make it a preferred material for constructing walls and floors in buildings where noise reduction is crucial. It is often used in hotels, hospitals, schools, and office buildings to enhance the acoustic environment.
- Ceilings: Installing lightweight concrete ceilings can also contribute to soundproofing, preventing noise from traveling between different floors of a building. This is particularly beneficial in multi-story residential buildings.
- Precast Elements:
- Blocks and Panels: Precast lightweight concrete blocks and panels are widely used in construction for their ease of installation and transport. These precast elements can be manufactured off-site and then transported to the construction site, speeding up the construction process and improving site safety.
- Architectural Features: Due to its moldability, lightweight concrete is used to create intricate architectural features such as cornices, window sills, and decorative panels. These features can enhance the aesthetic appeal of buildings while maintaining structural integrity.
- Marine Applications:
- Floating Docks: Lightweight concrete’s buoyancy makes it suitable for constructing floating docks and platforms. Its resistance to water absorption and saltwater makes it durable in marine environments, reducing maintenance costs and extending the lifespan of the structures.
- Maritime Structures: It is also used in the construction of maritime structures such as breakwaters, seawalls, and piers. Lightweight concrete’s ability to withstand harsh marine conditions while being easy to handle and install makes it an ideal choice for these applications.
- DIY Projects:
- Planters: One of the most popular DIY uses of lightweight concrete is in the creation of lightweight concrete pots and planters. These planters are durable, customizable, and can be designed to fit any space or aesthetic preference. They are particularly popular for indoor and balcony gardens where weight is a concern.
- Furniture: Lightweight concrete is increasingly being used to create bespoke furniture pieces such as tables, benches, and stools. The material’s versatility allows for a wide range of designs, from modern minimalist pieces to rustic, industrial-style furniture.
- Decorative Items: DIY enthusiasts use lightweight concrete to craft decorative items like sculptures, garden ornaments, and even countertops. Its ease of use and the ability to create detailed molds make it perfect for crafting unique and personalized items.
- Infrastructure Projects:
- Bridges and Overpasses: In infrastructure projects, lightweight concrete is used to reduce the dead load on bridges and overpasses. This can lead to more efficient designs and the use of lighter supporting structures, ultimately reducing construction costs.
- Tunnels: Lightweight concrete is used in tunnel linings to provide structural support while minimizing the load on the surrounding earth. Its insulation properties also help in controlling the internal environment of the tunnel.
- Roofing Solutions:
- Roof Tiles: Lightweight concrete roof tiles are popular due to their reduced weight, which decreases the load on the roof structure. These tiles can be designed to mimic traditional clay or slate tiles while offering superior durability and weather resistance.
- Roof Decks: Lightweight concrete is used in constructing roof decks, especially in commercial buildings. Its insulating properties help in maintaining indoor temperatures, reducing the energy required for heating and cooling.
- Rehabilitation and Retrofitting:
- Strengthening Structures: Lightweight concrete can be used in the rehabilitation and retrofitting of existing structures. By applying a layer of lightweight concrete, the load on the structure can be reduced while improving its thermal and acoustic properties.
- Earthquake-Resistant Buildings: In earthquake-prone areas, lightweight concrete is used to retrofit buildings to enhance their resistance to seismic activity. The reduced weight helps in minimizing the impact of earthquakes on the structure.
How to Make Lightweight Concrete
Creating lightweight concrete involves using specific lightweight aggregates and adjusting the mix design to achieve the desired properties. Here’s a comprehensive guide on how to make lightweight concrete:
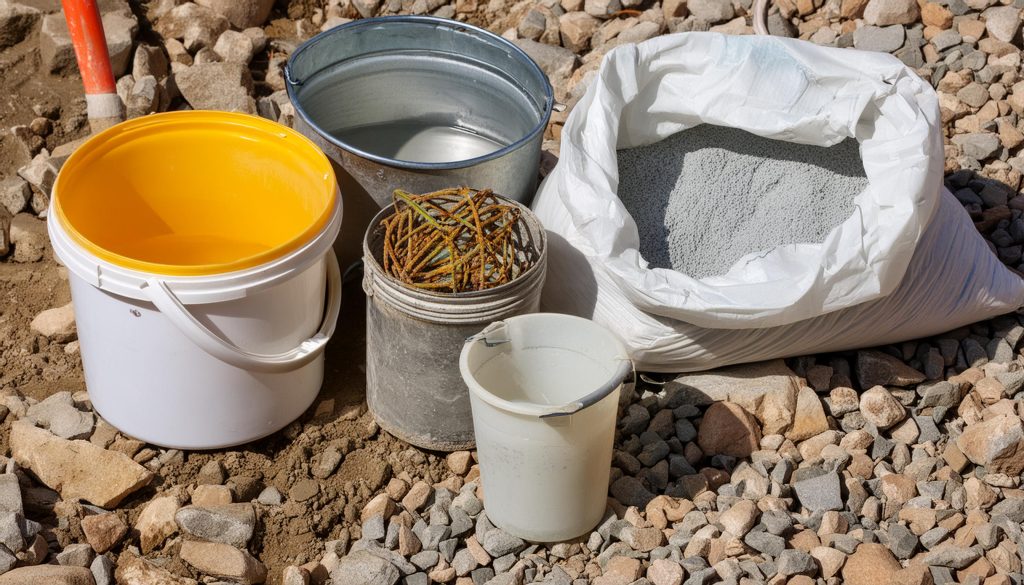
- Materials Needed:
- Cement: Portland cement is commonly used due to its strength and availability.
- Lightweight Aggregates: Options include expanded clay, perlite, vermiculite, pumice, and expanded polystyrene beads. These materials reduce the overall weight of the concrete.
- Water: Clean, potable water is essential for the mixing process.
- Admixtures: These are optional but can enhance specific properties of the concrete, such as workability, setting time, and strength. Common admixtures include superplasticizers, air-entraining agents, and water reducers.
- Reinforcement Materials: Depending on the application, you might need reinforcement such as glass fiber, steel mesh, or synthetic fibers to improve the tensile strength and durability of the concrete.
- Mixing Process:
- Step 1: Measure the Ingredients:
- Determine the required mix ratio based on the specific application. A common mix ratio for lightweight concrete might be 1 part cement to 2-4 parts lightweight aggregate by volume.
- For example, a basic lightweight concrete mix might use 1 part cement, 2 parts expanded clay aggregate, and enough water to achieve a workable consistency.
- Step 2: Mix the Dry Ingredients:
- Begin by mixing the dry ingredients (cement and lightweight aggregates) thoroughly. Ensure that the lightweight aggregates are evenly distributed throughout the mix. This step is crucial for achieving uniform strength and density in the final concrete.
- Step 3: Add Water Gradually:
- Slowly add water to the dry mix while continuously stirring. The amount of water needed will depend on the specific lightweight aggregate used and the desired consistency of the mix. Aim for a mix that is workable but not too wet, as excess water can weaken the concrete.
- If using perlite or vermiculite, be aware that these materials can absorb water, so you may need to adjust the water content accordingly.
- Step 4: Incorporate Admixtures:
- If using admixtures, add them according to the manufacturer’s instructions. Admixtures can help improve the workability, setting time, and durability of the concrete. For example, air-entraining agents can introduce tiny air bubbles into the mix, which can enhance the thermal insulation and freeze-thaw resistance of the concrete.
- Step 1: Measure the Ingredients:
- Mixing Techniques:
- Manual Mixing: For small batches, you can mix the ingredients manually in a wheelbarrow or mixing tub using a shovel or hoe. Ensure thorough mixing to achieve a uniform consistency.
- Mechanical Mixing: For larger batches or more consistent results, use a concrete mixer. Add the dry ingredients first, followed by water and admixtures. Allow the mixer to run for several minutes until the mixture is homogeneous.
- Pouring and Shaping:
- Preparation: Before pouring the lightweight concrete, prepare the molds or forms. Ensure they are clean and treated with a release agent if necessary to prevent the concrete from sticking.
- Pouring: Pour the mixed concrete into the prepared molds or forms. If working with larger projects, pour the concrete in layers, and compact each layer to remove air pockets and ensure proper bonding.
- Shaping: For decorative or detailed projects, use trowels, floats, or other tools to shape and smooth the surface of the concrete. You can also embed reinforcement materials at this stage if needed.
- Curing:
- Initial Curing: Allow the poured concrete to set undisturbed for the initial curing period. This typically takes 24-48 hours, depending on the ambient temperature and humidity. Cover the concrete with plastic sheeting or damp burlap to retain moisture and prevent rapid drying, which can lead to cracking.
- Extended Curing: After the initial curing period, continue to keep the concrete moist for an extended curing period. This can range from several days to a few weeks, depending on the specific mix and environmental conditions. Proper curing enhances the strength and durability of the concrete.
- Temperature Considerations: If working in hot or cold weather, take appropriate measures to control the curing environment. In hot weather, keep the concrete shaded and moist to prevent rapid drying. In cold weather, protect the concrete from freezing by using insulating blankets or heaters.
- Finishing Touches:
- De-molding: Once the concrete has cured sufficiently, carefully remove it from the molds or forms. If the forms were treated with a release agent, this process should be straightforward.
- Surface Treatment: Depending on the desired finish, you can apply additional surface treatments such as sealers, stains, or paints. Sealers can enhance the durability and appearance of the concrete, especially for outdoor applications.
- Polishing: For a smooth and glossy finish, you can polish the cured concrete using specialized concrete polishers. This is often done for countertops, furniture, and decorative items.
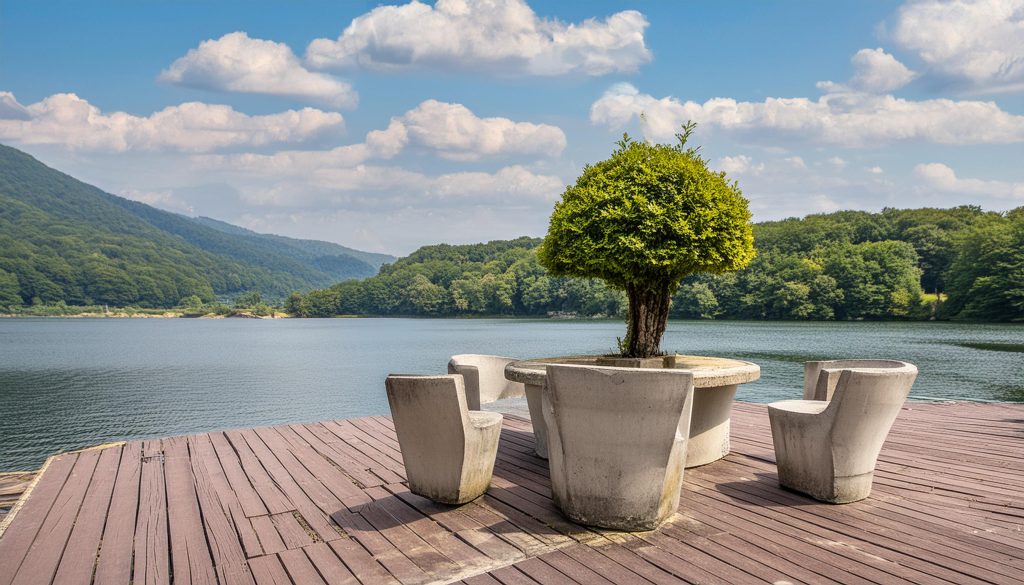
Practical Tips:
- Mix Ratio Adjustments: Adjust the mix ratio based on the specific requirements of your project. For example, increasing the proportion of lightweight aggregate can further reduce the weight of the concrete, but may also decrease its strength.
- Testing Samples: Before committing to a large batch, create small test samples to evaluate the mix’s workability, curing time, and final strength. This can help you fine-tune the mix design for optimal results.
- Safety Precautions: Always wear appropriate safety gear, including gloves, goggles, and a dust mask, when handling cement and lightweight aggregates. Work in a well-ventilated area to avoid inhaling dust and fumes.
Frequently Asked Questions
Q1: What is the density of lightweight concrete?
The density of lightweight concrete typically ranges from 300 to 1800 kg/m³, depending on the specific mix and application. For specific projects, the density can be adjusted using different lightweight aggregates and mix ratios.
Q2: Can lightweight concrete be used for structural purposes?
Yes, lightweight concrete can be used for structural purposes, provided it is designed and mixed correctly to meet the required strength specifications. Engineers often use it in buildings, bridges, and other infrastructure projects.
Q3: How does lightweight concrete provide insulation?
Lightweight concrete provides insulation due to its porous structure, which traps air and reduces heat transfer. This makes it an excellent choice for thermal and acoustic insulation, helping maintain indoor temperature and reduce noise.
Conclusion
Lightweight concrete is a versatile and innovative building material that offers numerous benefits, including reduced structural load, improved insulation, ease of handling, and eco-friendly options. Its applications range from building construction to DIY projects, making it a valuable choice for a wide variety of uses. By understanding the properties and advantages of lightweight concrete, you can make informed decisions for your next construction or DIY project, ensuring durability, efficiency, and sustainability.
The key benefits of lightweight concrete, including reduced structural load, improved insulation, ease of handling, versatility in design, and eco-friendliness, make it a preferred choice for various construction projects. Whether used in load-bearing walls, insulation panels, precast elements, marine structures, or DIY projects, lightweight concrete consistently delivers exceptional performance and durability.
In summary, lightweight concrete embodies the essence of modern construction practices—combining strength, versatility, and sustainability in a single material. Its continued advancement and widespread adoption promise to shape the future of construction, paving the way for innovative solutions that elevate both form and function in the built environment. As we look ahead, the potential of lightweight concrete remains boundless, offering endless opportunities for creativity, efficiency, and sustainability in construction projects around the world.
hello there, where can I get your products? I really need lighter pots.
This is a general article about lightweight concrete flower pots. However, it would be better to give some more specific details.